Different features are needed depending on the characteristics of the products. The processes used in our current products are SMT, Manual THT, Assembly, Coating, Software & Testing, Final control processes. Laser Automatic Line, THT Automatic Line, Coating Automatic Line will be decommissioned in the 4th quarter of 2023.
1. LASER PROCESS
In this process, QR codes are printed on the cards by laser burning method. With this barcode, traceability of the product is ensured. Other processes can also trace the product according to the card by taking this code as a reference. Cards whose QR codes are created with laser are automatically loaded into the magazines (carriers) at the machine exit, without human contact, with the existing machine system.
Currently, traceability is provided by labels issued after production, and the Laser line will be activated in the 4th quarter of 2023.
2. SMT PROCESS (SURFACE MOUNT TECHNOLOGY)
SMT Process is a process that includes five important processes. These processes are Printer (Solder Press Machine), SPI (Solder Press Test), Pick and Place (Typesetting), Reflow (Oven) and AOI (Optical control) processes.
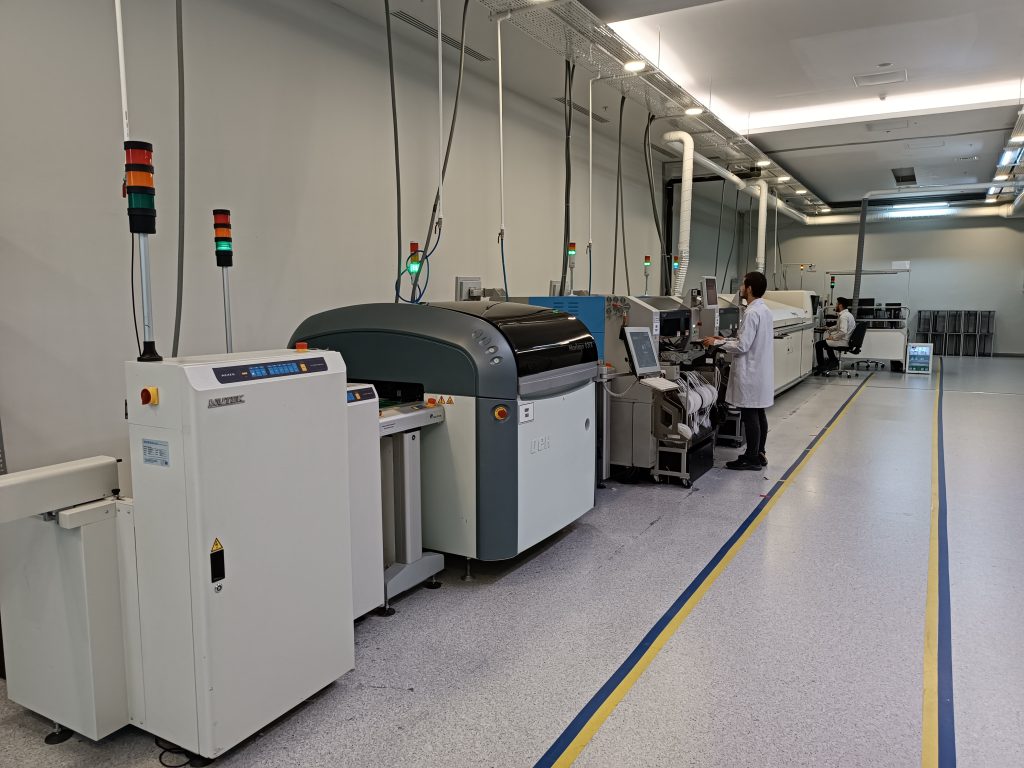
2.1. PCB Cleaner
Surface cleaning of PCBs in panel form is done here. (It will be put into operation in the 4th quarter of 2023)
2.2. Printer (Soldering Machine)
The soldering process is done here. Under humidity and temperature controls, solder is deposited into the solder islands on the card using a suitable sieve.
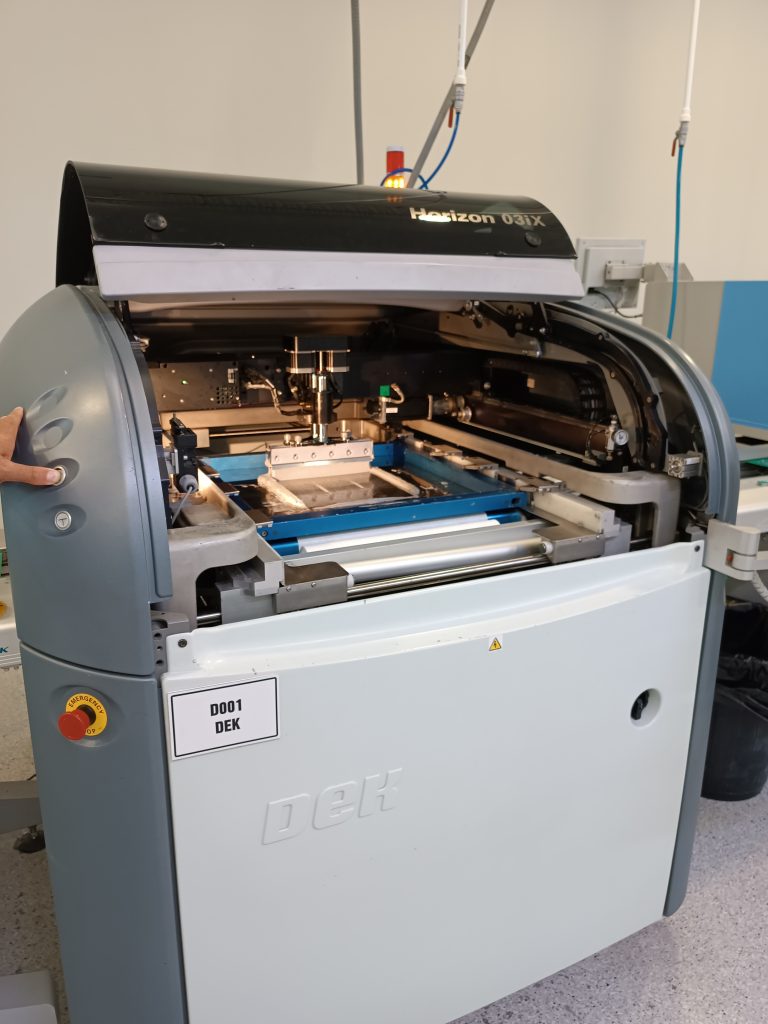
2.3. SPI (Solder Pressure Test)
The height, area, volume, short circuit and shiftiness of the solder applied to the island on the board are tested. (It will be put into operation in the 4th quarter of 2023)
2.4. Pick and Place (Setting Machine)
Placing of SMT materials on the card is done in this machine. With the verification system, incorrect material arrangement is prevented. The materials are fed into the machine quickly and automatically.
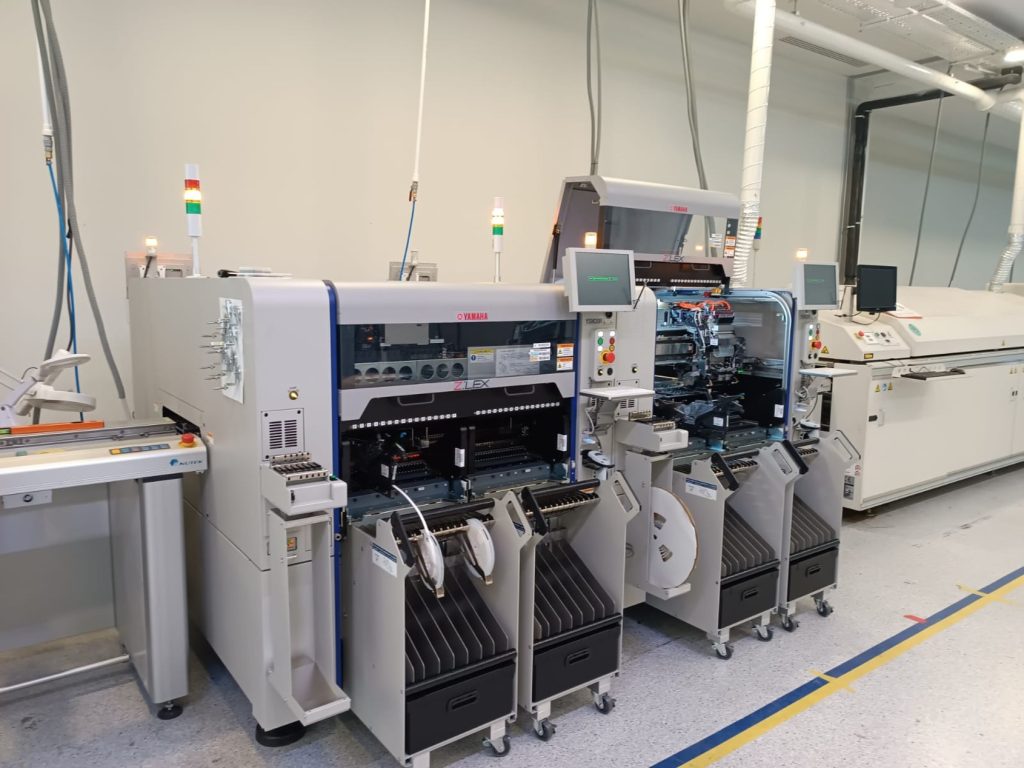
YS20 (Our new installed machine)
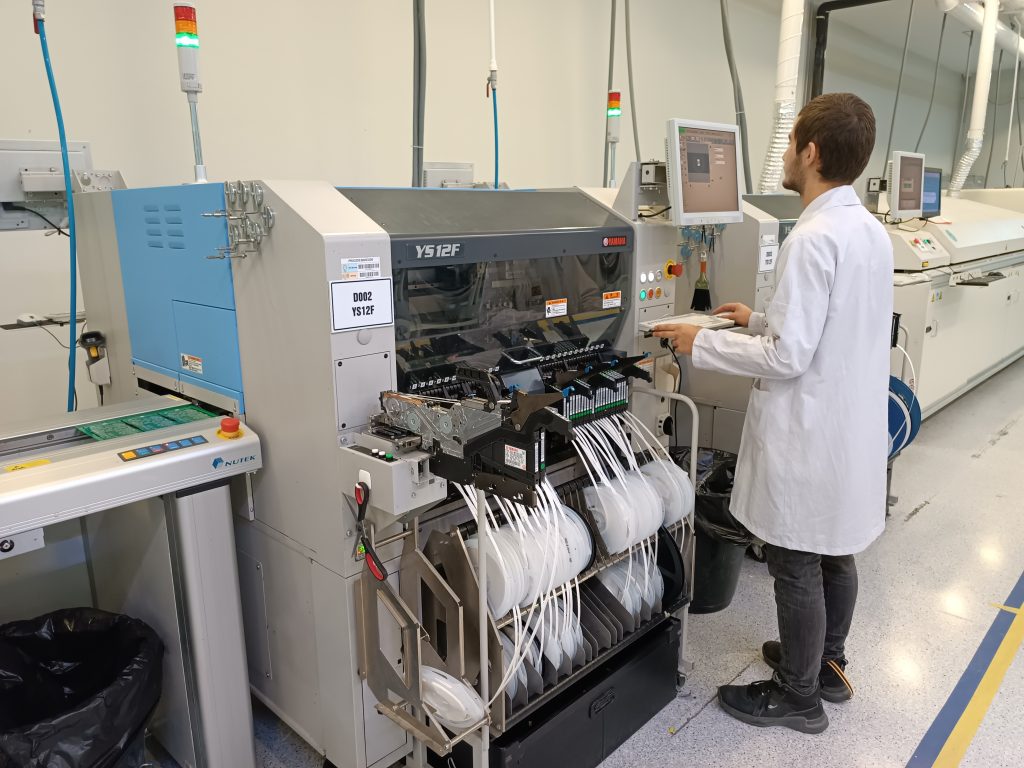
YS12 (Our old machine to be used in the prototype line)
2.5. Reflow
It is the activation and integration of the solder on the board with the solder island and material at appropriate temperature values and appropriate times. Thus, the materials are soldered to the card. The process takes place under a nitrogen atmosphere.
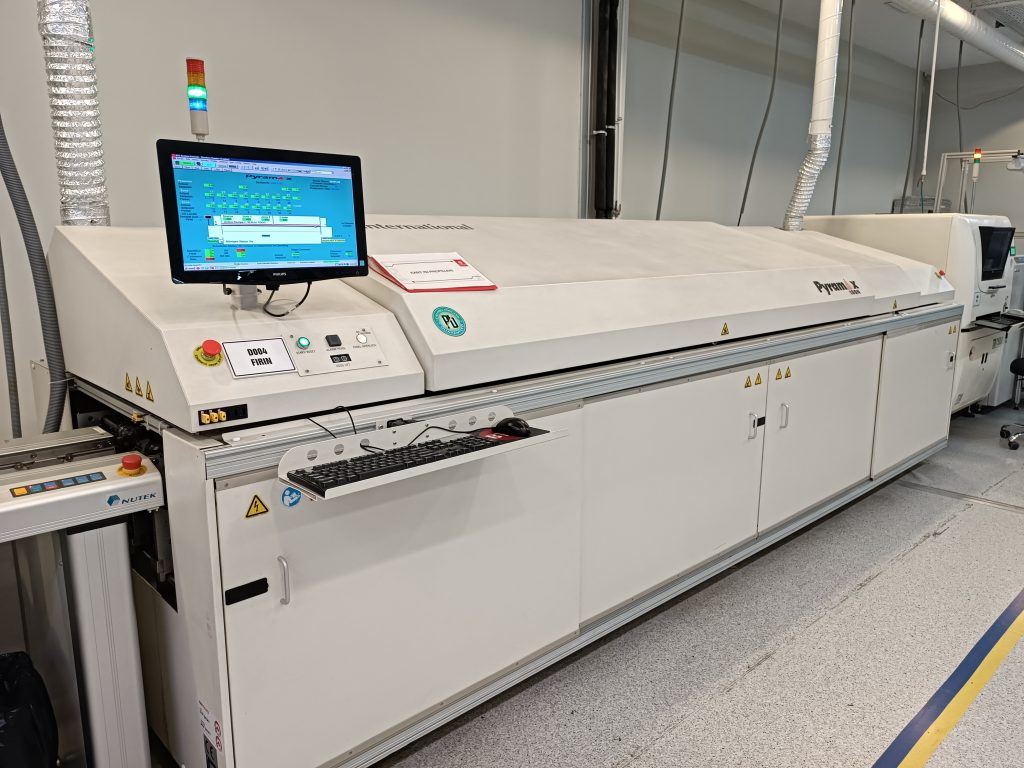
2.6. AOI
It performs two-dimensional automatic optical control. Cards whose typesetting or assembly has been completed are visually checked during this process. It checks the presence, direction, offset, height and solder condition of the materials and reports any errors, if any. (The process will be improved by installing a 3D machine in the 4th quarter of 2023)
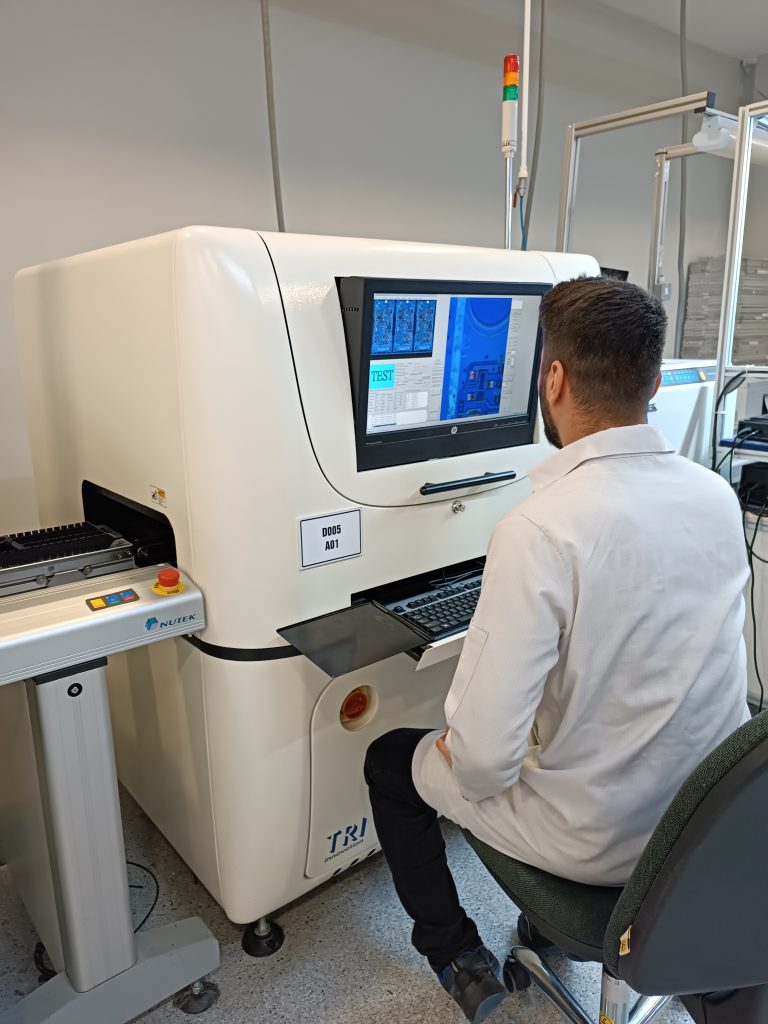
3. THT PROCESS (IN-HOLE MOUNTING TECHNOLOGY)
It means through-hole assembly technology, and the arrangement and soldering of legged materials are done in this process. We can divide this process into four: Radial, Axial, Selective Soldering and Pin Driving. (THT automatic line will be put into operation in the 4th quarter of 2023.)
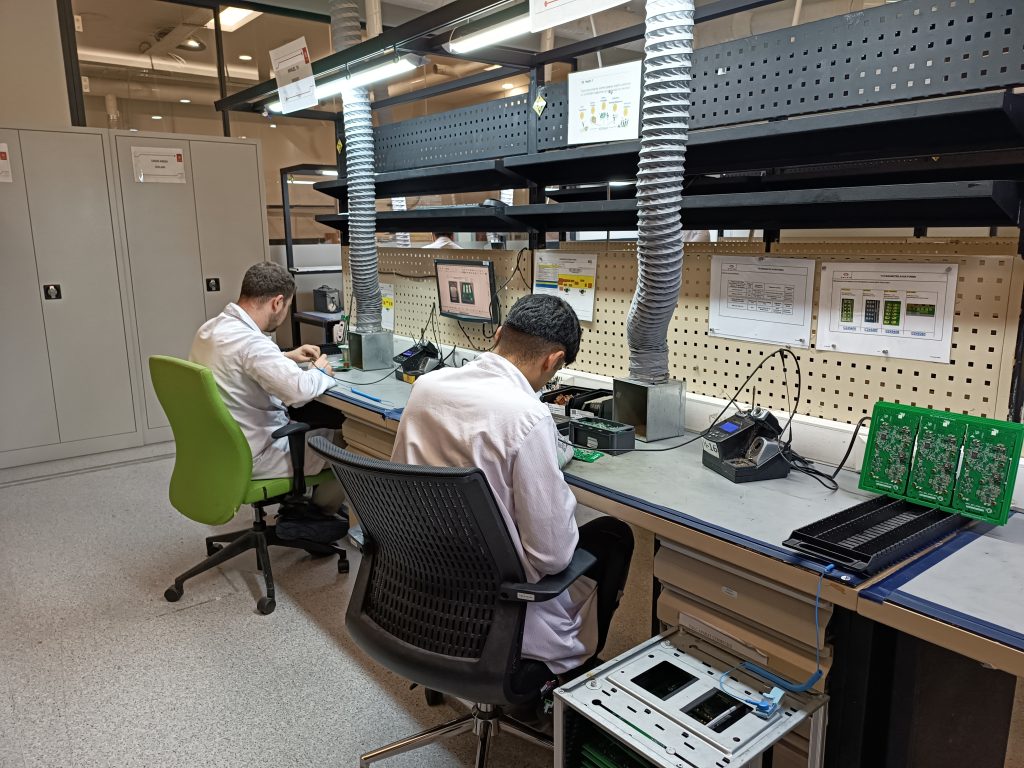
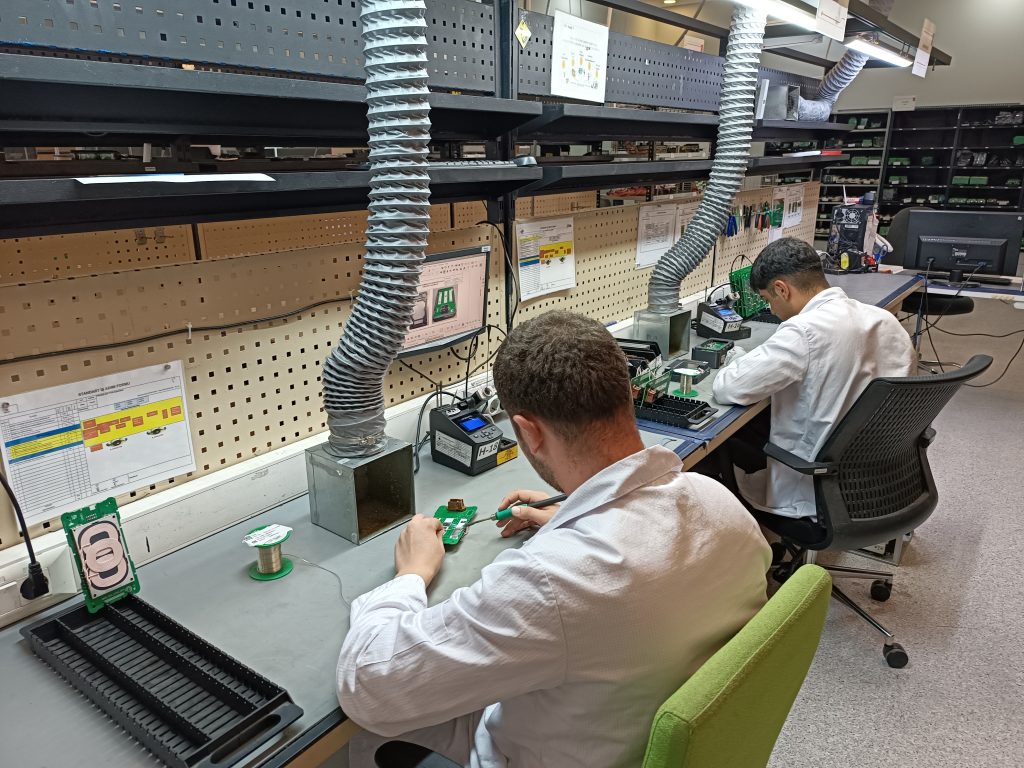
4. DISPENSER
It is used to apply substances such as protectors, adhesives, coatings, etc. to desired points on the card, according to customer request.
5. COATING (CONFORMAL COATING)
In order to increase the resistance of the cards against environmental influences, regional protective coating is applied according to customer request. (The coating automatic line will be commissioned in the 4th quarter of 2023.)
6. FCT
Electrical and functional tests of the cards are performed in this process. In this process, the values, directions, existence, currents, voltages and functions of the materials are checked. LED Tests are applied in functional testing and color, brightness and homogeneity controls are made.
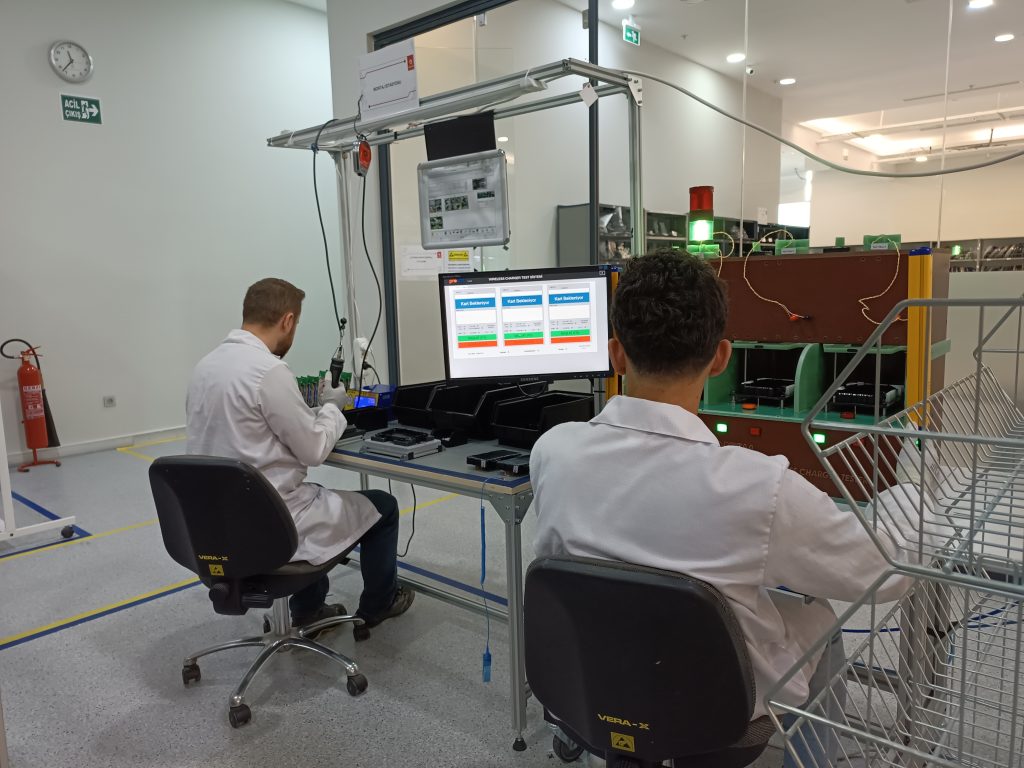
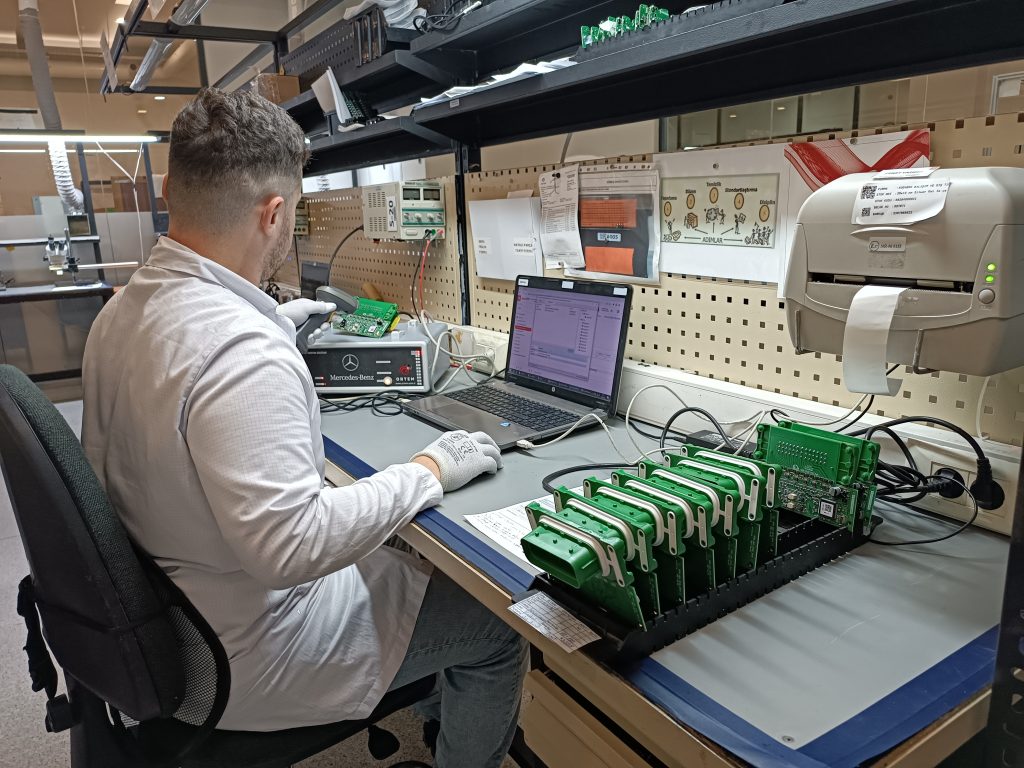
7. ASSEMBLY & FINAL CHECK
In this process, assembly and visual control are performed. Scratches, cuts, deformed cards or materials that may occur on the lines or be overlooked are detected thanks to this process.
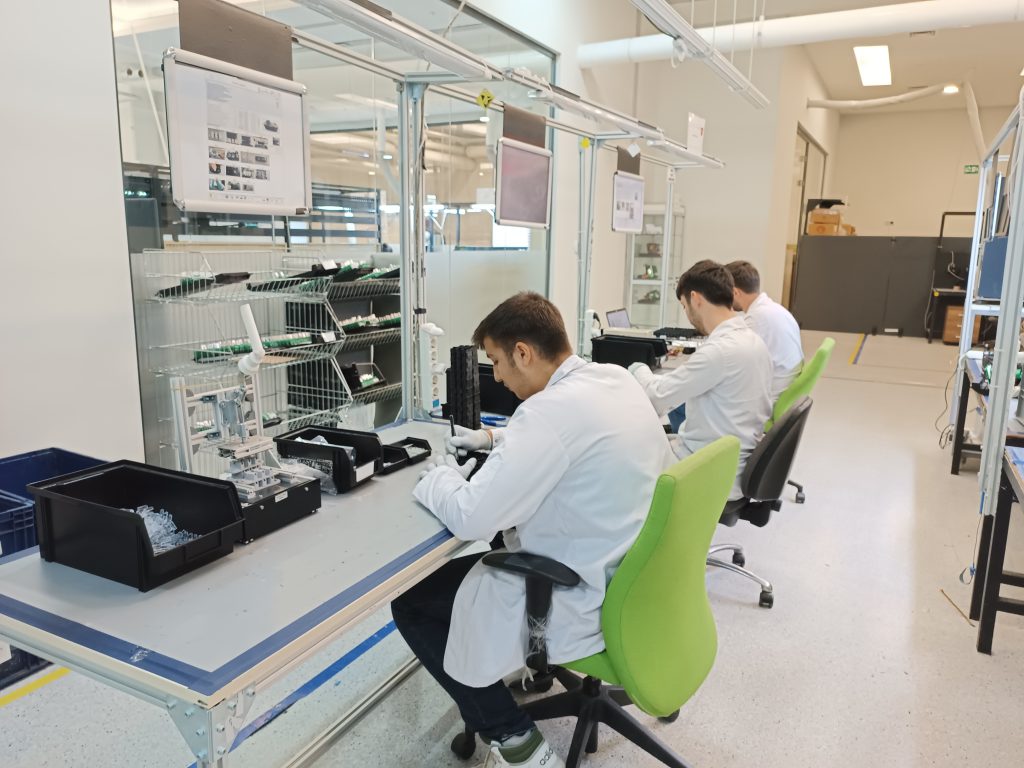
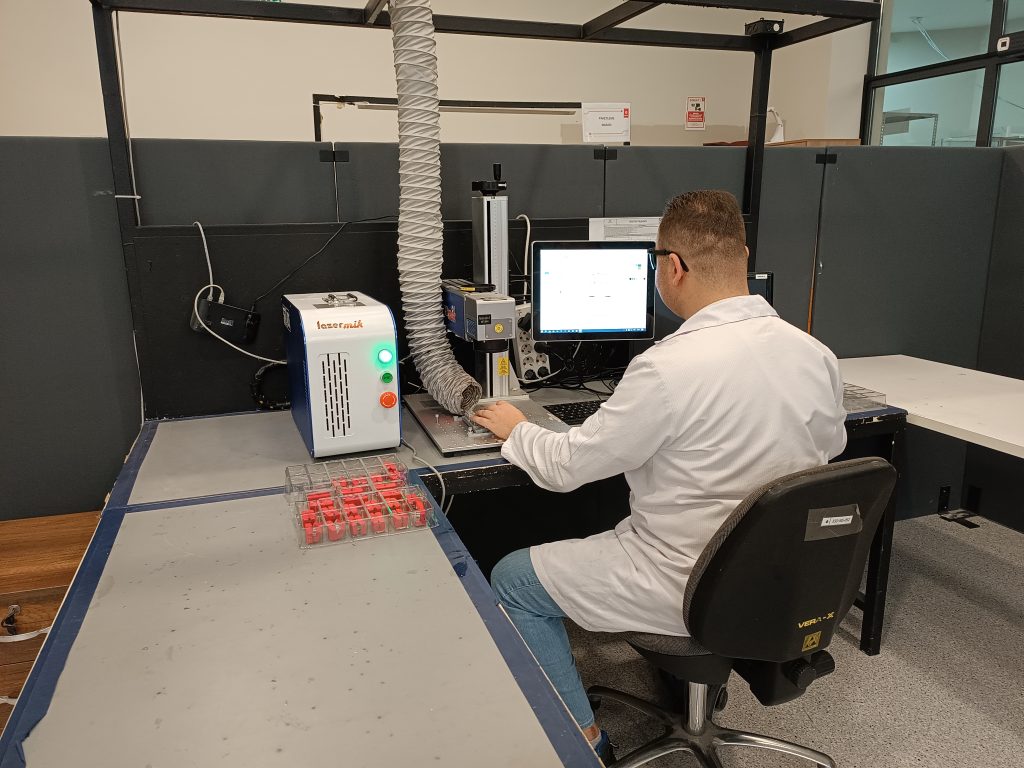
Laser Process
8. PACKAGING
PCBs are set according to the customer’s request and packaged according to the customer’s request.